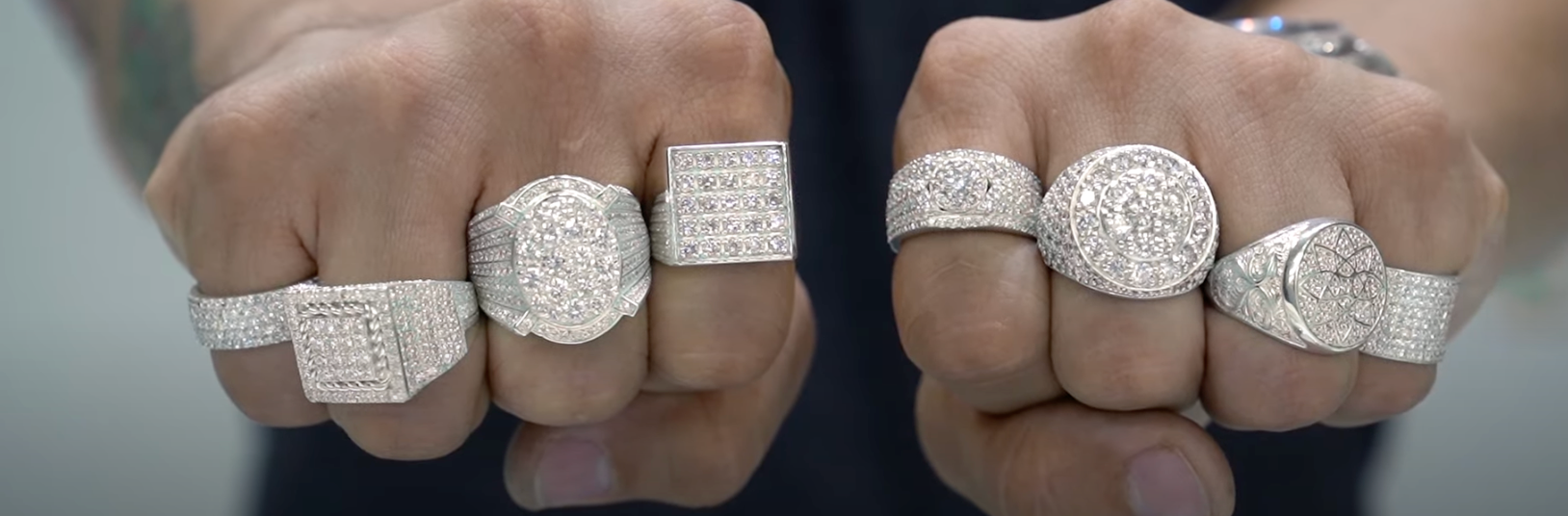
How Silver Rings with Diamonds Are Made | Step-by-Step Ringmaking
How are silver rings made? Learn the step-by-step process from 3D printing and casting, to the final touches. And they end up right here, where you can come down to Miami yourself, shake our hands, buy it here or buy it online.